製造業にDXを取り入れることで得られる3つの効果
身近なところから始めた事例を参考にしよう
ナレッジ
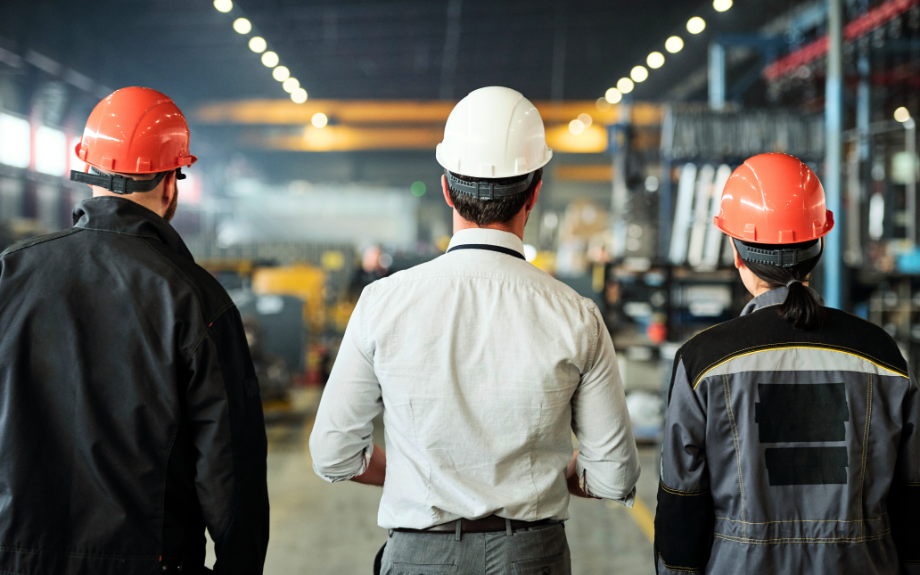
目次
日本ではDXの導入が業種を問わず課題になっていますが、それで一体何ができるのか?と具体的なイメージが沸かない方も多いことでしょう。
しかし、デジタル技術の導入を積極的に行う企業は、製造業の根幹に関わるところで様々な恩恵を受けています。
そこで今回は、中小事業者のDXへの取り組みとその効果を紹介します。
みなさんの会社との共通点を探しながら、ぜひ参考にしてみてください。
日米でこんなに違う!DXへの意識
IPA(独立行政法人情報処理推進機構)が発行した2021年の「DX白書」では、DX戦略などの現状について、日米比較を軸に紹介されています。
浮き彫りになっているのは、日米での意識の大きな違いです。
白書でまず紹介されているのは、DXの進捗状況についてです。

(出所:「DX白書2021」独立行政法人情報処理推進機構)
https://www.ipa.go.jp/files/000093699.pdf p2
「取り組んでいない」とする企業の割合はアメリカでは14.1%であるのに対し、日本では33.9%、3割以上にのぼっています。
業種別にみると、図2のようになっています。
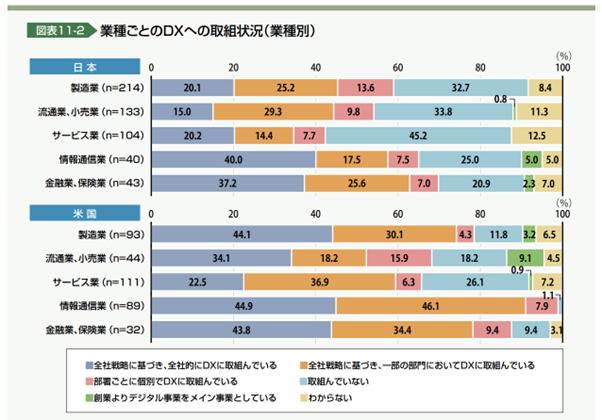
(出所:「DX白書2021」情報処理推進機構)
https://www.ipa.go.jp/files/000093699.pdf p3
アメリカの製造業で「取り組んでいない」と回答している企業の割合は11.8%であるのに対し、日本ではその3倍近くである32.7%にのぼっています。
アメリカと比べて意味があるのか?と他人事に感じる方もいらっしゃるかもしれませんが、日本は世界的に高齢化が顕著な国です。
人口構成の違いを考えれば圧倒的不利と言えるのにデジタル化が進まないままでは、世界的に取り残された状況になりかねません。
デジタルへの苦手意識をなくすたった一つの方法
なお、DXを考える時に欠かせないスタンスがあります。
それは、「DXでいったい何ができるのか?」という問い方ではなく、「今ある自社の課題をDXでどう解決できるか?」というアプローチです。
DXについて考えることは同時に、今ある自社の課題を洗い出す大きなチャンスでもあります。
それぞれのITサービスの名前や機能に踊らされるのではなく、「まず何を解決したいか」ということから始める必要があります。
この発想の転換があるかどうかが、DXを理解できるかどうかの分かれ目です。逆に言えば、自社の課題を洗い出したいという気持ちさえあれば、そう難しく考える必要もありません。
製造業がDXで得た3つの効果
実際に、中小製造業でのDXの成功事例をみていきましょう。
おもに「生産性の向上」「技術者の早期育成」「BCP(事業継続計画)」の3つの効果があります。それぞれご紹介します。
生産性の向上〜従業員の不満解消と生産数5倍を同時実現
まず北九州市のチョコレート製造業、オーエーセンター株式会社のケースです*1。
3つの事業を展開していますが、そのうちのひとつがチョコレート菓子「ネジチョコ」の製造販売です。
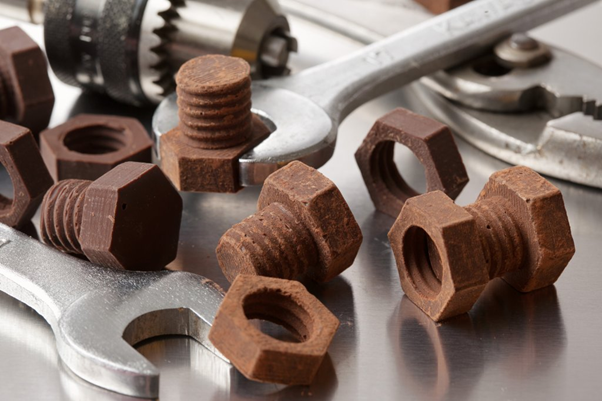
(出所:「【福岡発】実際に締まるネジチョコ、新たな定番お土産を作った「地元愛」」経済産業省METI Journal)
https://journal.meti.go.jp/p/32483/
チョコレートなのにボルトとナットが実際に締まるというもので、八幡製鉄所の関連施設が世界文化遺産に登録されたことを機に「鉄の街」をイメージして開発された土産品です。
3Dプリンタで作った型を利用していますが、固まったチョコレートを型から抜き、ボルトとナットがペアになるように袋に入れ、検品し、箱詰めをし、出荷する、という工程をすべて手作業で行っていました。
しかしYouTubeなどで取り上げられて人気に火がつき、生産現場が限界を迎えてしまいます。従業員を増やしてなんとか1日に6000個を生産できるようにしましたが、それでも現場の従業員の負担は大きく、不満が噴出するという課題に直面しました。
実際に動く精巧な商品であるため、チョコレートを流し入れる力加減や型抜きには神経を使います。製造数を増やしたことで従業員の集中力が限界を迎えてしまう、腱鞘炎になる従業員が続出する、といったトラブルが発生してしまいます。
ただ、企業としては、せっかくのブームを逃すわけにはいかないことでしょう。
そこで取り入れたのがデジタルの力です。生産の完全自動化を目指しました。
チョコレートを型抜きするロボット、チョコレートの自動充填機といった、従業員が神経を尖らせる「一定の力加減」を実現してくれる機器の他、検品にはセンサーを導入しました。
そして、従業員の負担軽減だけでない効果をもたらします。
機械に内蔵されているコンピューターでスピード調整や生産量の実績の記録が可能になったのです。
在庫管理もバーコードスキャナーに切り替えるなど工場全体にデジタルを導入した結果、手作業の限界だった6000個の5倍、1日に3万個の生産が可能になりました。
商機を逃さないためにも従業員の負担を軽減し、事業を成長させた事例といえるでしょう。
技術者の早期育成〜言葉にしにくい熟練者の意図を可視化
また、長い伝統を持つ職人の世界でも、デジタルを取り入れた事例があります。
岩手県で伝統工芸品の南部鉄器を製造する盛岡市のタヤマスタジオは、ベテラン職人の思考を再現するAIの開発を進めています*2。
若手が熟練者から素早く学べるようになり、従来は10年程度かかっていた下積み期間の短縮に繋げたいという考えです。
まず熟練者から製造の際に重視しているポイントを聞き取り、南部鉄器に関するキーワードを選んでいきました。キーワードごとに関連する要素も含めてデータ化することで、熟練者が考えていることを可視化するというものです。
若手が熟練者から学ぼうとした時、例えばデザインを見せた時に修正点を伝えられることがあります。しかしそれが断片的な言葉でのコミュニケーションになってしまい、若手が指示の意図を正確に理解できなかったという課題を解消するための取り組みです。
技術の世界では、なかなか言葉での表現が難しい要素も多いことでしょう。しかし「断片的な言葉」をAIに入力することで、言葉の背景にある熟練者の思考を探ることができるというものです。
職人の育成期間を短くすることで、海外など幅広い市場からの需要に応えていくこともできます。少子化への対応にも繋がることでしょう。
BCP〜受発注のデジタル化がコロナ禍での生産を支えた
さて、いま、災害など非常事態が発生した時にどのように中核事業を続けていくかあらかじめ計画しておく、BCPの策定の重要性が増しています。
デジタル化によってコロナ禍をくぐり抜けたという企業事例もあります。
岐阜県・関市の中央工機株式会社はガスや石油機器などの部品を製造していますが、扱う製品の種類は多く、1日に1000品目以上の部品を生産しています*3。
受発注を電話やファックス、メールで行っている中小企業は多いことでしょう。しかしそれらは人に依存する方法で、電話の場合は聞き間違えてしまったり、メモを取ったとしても書き間違えたり、といったリスクが残ります。
特に多品種を扱う企業となると受発注のやりとりは多く、事務の負担が大きくなりがちです。
そこで2000年代初頭から、契約書類や受発注の詳細などを、専用の通信回線を使ってデータでやりとりするシステムを導入しています。
EDI(Electronic Data Interchange)と呼ばれる手法で、大量のやりとりでもミスが起きる可能性は低くなり、同時に事務作業の負担を減らすことができます。
早期からEDIの導入や生産管理のデジタル化を進めてきた結果は、コロナ禍での対応に反映されました。事務などの間接部門を効率化している分、生産部門に人員を手厚く配置できていたため、一部の従業員が出勤できなくなっても生産を続けられたのです。
従業員にもデジタルへの慣れがあり、リモートワークも実現しています。さらにリモートワークの導入を機に、出産・育児で離職して地元を離れていた従業員を再就職させることができました。貴重な人材の確保にもつながっています。
補助金の利活用も検討しよう
ここまで、製造業がデジタルで得られる効果を3つに分けてご紹介してきました。
いずれの会社にも共通しているのは、「目の前の課題」や「特定の課題」の解決に向けたデジタルの導入から始まっているというところです。
DXやIT化を「なんでも便利になる道具なんだろう」と漠然と捉えているままでは先には進めません。試してみたとしても中途半端な導入になってしまい、誰も得をしないという結果にもなりかねません。
DXへの一歩は、まず最優先で解消しなければならない課題は何なのか検証することから始める必要があります。結果として仮にデジタルの導入にすぐには至らなかったとしても、課題の洗い出しは会社として常に必要なことですから、良いきっかけになることでしょう。
なお、2024年もIT導入補助金が設置されています*4。
行政や自治体の補助金を有効活用することも積極的に検討したいものです。
参考文献
*1
「日本公庫総研レポート No.2022-5 デジタル化で生産性向上を図る中小製造業」日本政策金融公庫
https://www.jfc.go.jp/n/findings/pdf/soukenrepo_22_12_09.pdf p25-26
*2
「南部鉄器職人の思考をAIで再現 後世への技能伝承を高速化」日経クロステック
https://xtech.nikkei.com/atcl/nxt/column/18/01880/121300005/
*3
「日本公庫総研レポート No.2022-5 デジタル化で生産性向上を図る中小製造業」日本政策金融公庫
https://www.jfc.go.jp/n/findings/pdf/soukenrepo_22_12_09.pdf p12-14
*4
「IT導入補助金2024」公式サイト
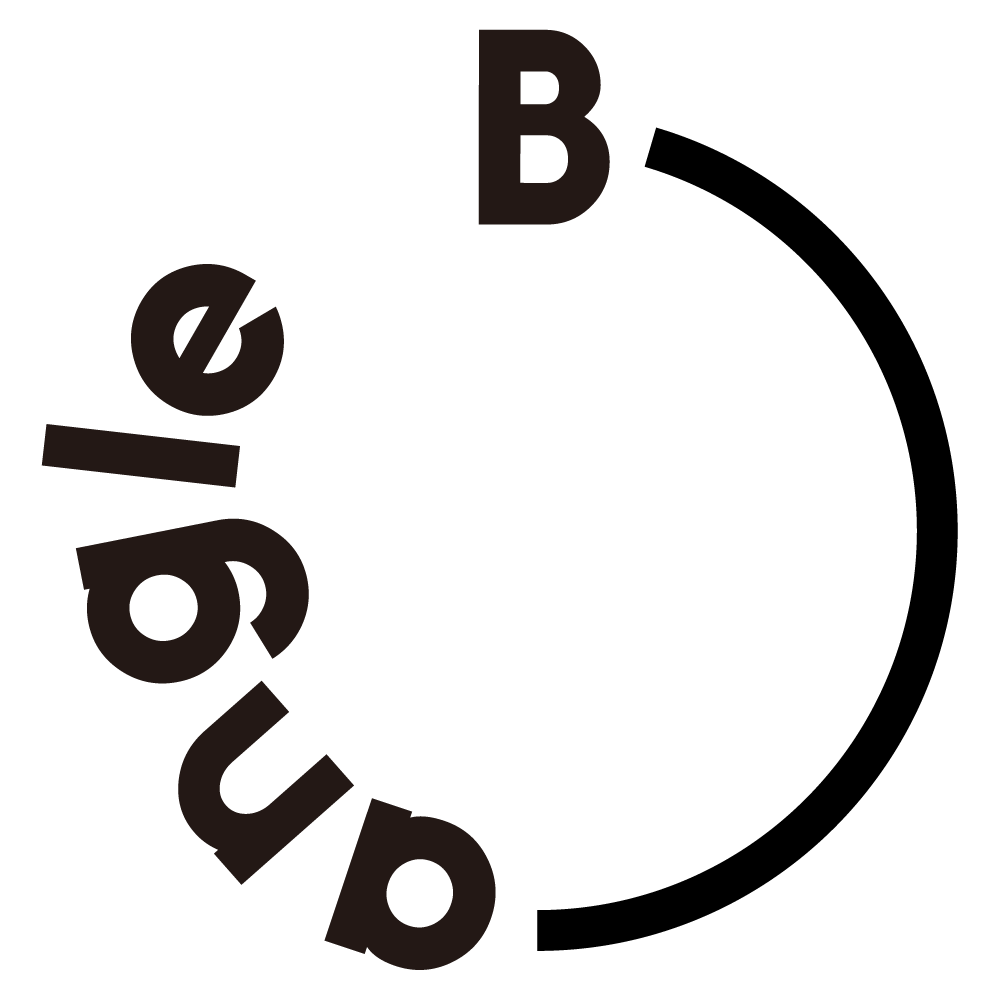
フリーライター
清水 沙矢香 Sayaka Shimizu
2002年京都大学理学部卒業後、TBSに主に報道記者として勤務。社会部記者として事件・事故、テクノロジー、経済部記者として各種市場・産業など幅広く取材、その後フリー。 取材経験や各種統計の分析を元に多数メディアに寄稿中。